Now Get More Energy. The SYSTEMA ENERGY.
Gungho Cowboy
27 Oct 2009
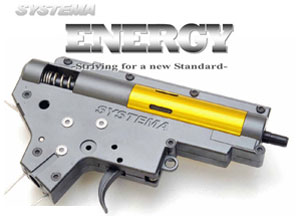
Optimus Prime is on a personal leave for a project, business, plus personal so it's tough to get in touch with him nowdays. This leaves me with some dumped emails that I need to put my attention during my free time, which is rare. However, the autoforward of some un-spam checked emails at the editorial email do go forward to me for this period. And scanning some of this is information about the SYSTEMA ENERGY and here's what Systema has to say:
"At the inception of SYSTEMA, it was our utmost priority to create parts that were strong and durable. On the other hand, with an increase in the strength of each component so too did the individual weight, which at one point exceeded over 600g for a completed Mecha Box weight in comparison to an OEM version; after installation this caused a hindrance in the handling of the AEG. At one point in time when resin based outer AEG components were popular, the nucleus of the AEG (Mecha Box) complimented the overall weight and feel, however when the focus shifted to a more “Real-Steel” replicated external receivers’ the overall weight became a obstruction to the active gamer. Therefore, after 12 years have passed we decided to completely revamp our SYSTEMA parts with our most important development theme to be the lightening of the weight for each component. In order to realize our theme, we not only changed the materials used to create the parts, but also applied the knowledge and wisdom of various techniques that we have accumulated throughout these years to make this concept a reality.
It was known to us that certain issues existed yet we were not able to find an effective solution in the past; problems such as the dragging feel of the trigger after the trigger switch is off due to the residual inertia stemming from the gear set, as well as a loss of durability on the Piston caused by the heavy Sector Gear. We decided to approach and carefully inspect each of these issues stemming from weight one by one and the fruits of our labor have brought forth our newest design ENERGY.
To be specific, we replaced all of our conventional parts which we originally believed to have been superior in strength with a lighter, hollow structured sintered product, and for the components that bears any load (such as all of our gears) we reinforced it by adding a heat treatment process. Due to the nature of the Sector Gear requiring durability yet a strong focus on light weight, special NC processing was undertaken to the small gear teeth section prior to assembly. Likewise, due to the NC processing much of the large Sector Gear teeth area have also been removed therefore to maintain the balance of strength, Dry Carbon panels have been press fitted onto that section. Our Spur /Helical Gear are our new concept.
By making the module smaller we were not only able to improve the torque slow down ratio, but at the same time by changing the helical angle to 45 degrees we were able to disperse the heavy load typically placed on a single tooth. The Helical Gear for the AEG was created to provide a durable yet strong torque gear set application within the predetermined space of the Mecha Box; and so there were various ideas imbedded in the gear to make this possible. With our revamped version we were able to adopt a gear tooth link structure between the Spur Gear and the Sector Gear (which comparatively speaking has a small slow down ratio) that lightens the cycling thus in turn allows for an improvement in trigger response. In addition, when the gear set is at a mid-cycle position and the electrical current is cut, a strong shearing action takes place, however we are able to secure a strong and stable gear set with our one piece cast die molded components.
For the new Bevel Gear, based on the results acquired from our P.T.W. we adopted the highly precise gear that we refer to as module 0.5. Naturally, our newly developed gear set has a greatly improved torque slow-down ratio, which is a mid-torque ratio between our conventional Ultra-Torque Up and our Super Torque Up versions. With the introduction of our die mold processing for our module as well as our careful heat treatment processing to maintain strength and durability in our gears, along with the new addition of our Chrome Molybdenum Motor Pinion as a set you can experience an even smoother gear linking thus help reducing overall noise.
MULTIFUNCTION
For those who purchased an AEG, based on their imagination it is possible to create their very own special custom AEG, and to help make that a reality was what gave birth to our SYSTEMA variation of parts.
However to follow the theme of our new renewal (based on “light weight”) we decided to cut out any part variation without hesitation that does not meet that criteria. Within those variations are a few parts that many have come to favor, however we will completely reform them as well as put together the reasons for that decision later. Although, the design change appears minimal, the functionality will be improved significantly.
As one example, would be our ENERGY Piston Head.
Our much favored silent Piston Head is our fundamental design; however we changed our Piston Head Base as well as the bumper portion to allow the Piston Head to turn.
As a default, the conventional Piston uses 6 ports for the Piston Head which aids the BB into the loading chamber via a suction action when the Piston recedes, however it is now possible (with our newest design) to change the air inlet ports to either 6, 4, or 3 ports to control the suction strength. By changing the number of air inlet ports, it gives the player more control over how much pressure is desired within the cylinder thus allowing the player with greater control of their specific playing needs.
Our rough plan focuses on the small receptacle of the magazine spring housing within the drum of the magazine, causing loading problems. Three points within the MP-5 Series. Four points for resin made magazine cases such as the SIG and AUG Series. Six points that we feel appropriate to address for the G-3 and M-16 Series.
We stumbled upon a good idea while developing our P.T.W. series where grease tends to affix itself better with products that were lathe processed, which we put to use in our ENERGY Cylinders; there are 5 varieties ranging from TYPE 0 ~ TYPE 4.
The functional characteristic of our conventional Cylinders had either a Teflon or NB plating that lowered resistance improving the piston movement speed. However during use it became apparent that within the Cylinder itself, the grease used to maintain an airtight seal would deviate towards both ends of the cylinder, thus during prolonged use adequate performance could not be maintained. As a result, during our trial experiment we added various small pitches grazes within the Cylinder with the lathe and after careful inspection we were able to secure sufficient levels of grease within the Cylinder walls.
As a result we chose a module with a pitch that is a bit coarser than the P.T.W. to mass produce our new Cylinder. Even the conventional press fit air inlet port has also undergone NC processing to lessen the wear on the O-Ring. Instead of having similar colors, we chose different and bright colors to identify the various versions of our Cylinders. Although those parts may appear to be simple, for the AEG this part has the greatest effect on conversion efficiency of energy. We are proud to release our newest creation [ENERGY Cylinder]; please give this a try.
Value Price
At one point we demonstrated by slightly changing cross section of the exhaust port (nozzle air outlet area) would have a direct correlation to the power output with our Bore-Up Cylinder Set.
To put that concept to good use as well as to create a cylinder head that is compatible with various spring tensions we came up with our newest cylinder head. Furthermore, to make our product friendly for use in cold districts, we changed the O-Ring just to be certain.
Expandability
These new parts that we have introduced are considered the nucleus of the custom parts, and we will be selling sets that includes these parts at the same time.
To match each model with the most suitable and efficient air suction / exhaust combination we will release an exclusive cylinder set. 3 Gear Set types that is compatible with various spring types. Above all, to meet our renewal theme of “Light Weight” we would like everyone to feel our [NEW Complete Mecha-Box (NEW CMB)].
The case used for the C.M.B. differs a bit in tangent to the principle concept; as instead of the purpose o it being light in weight we focused on designing a case that controls noise emanating from the Mecha box. With the residual parts being light in weight versus the case, the purpose for each component became much clearer. Working within a rather weighty case lay very light and nimble parts; this produces a new feeling that can be enjoyed when firing. By all means, we ask that you give this a try.
Final Thoughts
SYSTEMA parts are an embodiment of our company policy which is [to create products closest to our customers]. We were able to develop our T.W. series with the support of our customers throughout the world. Because of that support we were able to grow our series all the way to our SUPER MAX version. Although that is considered top grade in performance and quality in today’s marketplace, we take pride in the creation of all of our products (all the way to our shim set); we place the same level of care as our T.W. with everything that we make.
We ask that you try our latest SYSTEMA parts and confirm for yourself the level of gratitude that we embed into our products.
Introduction of the ENERGY Motor
The development concept of our newly released ENERGY Motor is: Ease of use with great performance. In order to better explain what embodies our development concept for our newest ENERGY Motor, we would like to introduce our newest motor while comparing our other two very popular TURBO and MAGNUM motors.
1. Maximum Tolerated Voltage
The original power source for the TM AEG (motor) came from R/C technology. After repeated improvements to the motor; several improvements were gained; however the primary goal itself had not changed: “Improve the torque characteristic based on a constant voltage, to decrease the consumption of electricity.” Our primary objective for the development of our products has always been: “The improvement of the performance of our products through the advancement of technology.” It is because of this principle; the performance that we seek in our motor is fundamentally different from other companies. One example is in the difference of the fixed voltage rating.
The rating refers to, at the time of development of this product, the standard of the voltage was set; ironically this is also will refer to the product’s conditional limit as well.
In the case of the AEG Motor (to be specific), the maximum tolerated battery voltage, the maximum allowed current flow through the motor, as well as the maximum allowed cyclic turn ratio are all pre-set during the design stages of development for the motor. Therefore, assuming that a motor (including an OEM version) was designed for the 8.4V / 1300mAh battery, the principle performance as well as durability is only guaranteed up to the specified rating. In contrast, our motor voltage rating is set at 12V. For a custom motor, this is an obvious choice for our voltage rating, to make that value a reality we added extensive work such as; the use of superior heat resistant materials for our rotor coils, as well as incorporating 30% silver for our Carbon brushes.
2. Motor Case
For the motor; unlike the magnet used, not much is known to the public about the value of the motor case itself, however there is a significant difference in the overall performance of the motor depending on the density of the magnetism versus the thickness of the case. For a mold pressed product, the thicker the product is required to be, naturally the more difficult it is to manufacture at the time of processing. Generally, it is common to see press sheets of steel of 0.8~1mm in thickness to be used; however our company traditionally uses 1.2mm thick sheets of steel. In the event that the steel sheets are thick, when the inner portion is stretched; the dimension neither causes the magnet volume to shrink nor change the outer dimension of the rotor, but rather will aid in torque by assimilating the gap between the magnet and the rotor. This method can only be possible through very strict dimension management during the production of our cases.
3. Ag 30% (Silver) Carbon Brush (New Brush Case)
In our development concept of “Easy to use with great performance” also includes very durable performance as well. There are many diverse tuning menus out there today ranging from extreme high speed tuning of 30 rounds per second to power customs where high tension springs exceed M150. Of these various situations; in terms of durability the Carbon Brush is definitely the best in its performance. It has been known for a long period of time that high levels of electrical current can be secured with the incorporation of Silver. However due to time and cost issues many have given up on this proposition. Furthermore, by adding more Silver content simply will not enhance the overall performance. We performed many experiments with various amounts of Silver content brushes for an AEG application, and have concluded that 30% Silver content to be the most effective.
In addition, in order for the Brush Commutator to clear over the gap (in essence, dodging the slight vibration continually); every particular dimension within the Brush Case must have strict size tolerances maintained and above all experience in maintaining those tolerances as well. What makes or breaks the performance of the Brush is the production technology of the Brush Case which is our most important point.
4. The difference between the TURBO and MAGNUM
We are receiving great response to our TURBO and MAGNUM Motor series, which our development concept was to: “Using the technology from our T.W. 490 Motor; do our best to create a high performance motor.”
The results were very good, with a hand wound Rotor to produce a high cyclic balance, along with a combination of our high torque producing Neodymium Magnet, and our highly heat resistant Aluminum End Bell, we put together all of our best technological attributes into our high performance custom motor which we feel surpasses the conventional notion of the custom motor. Although these two special motors are capable of expressing their exceptional traits, at the same time; in order for that to come to fruition certain conditions surrounding the motor need to be met; such as the capacity of the battery, some of these conditions may in fact be significant.
This time around, we reflected heavily into this and instead of focusing on either power or speed we decided to shift in creating a motor that is more durable for use in standard airsoft game scenarios.
Some people may misunderstand this as something of the ordinary, however we made sure that our motor has important points such as easily replaceable components (once they are worn out), modified motor (disassembly possible), as well as Ag 30 Carbon Brush (as mentioned above); all of these important points we incorporated into our newest motor to extend the overall durability.
We will mention the details of the performance later, however we can say that our motor is able to deal with the torque produced by various battery capacities, capable of high adaptability while producing a flat torque, also has similar qualities in complimenting various spring tensions.
As opposed to either an extremely strong or fast application with limited conditions set, with the TURBO or the MAGNUM Motor being the only motors that are capable of performing; the ENERGY Motor in contrast is a high performing long lasting and extremely stable motor for all other applications. Our clear and well developed product is our proud edition to our selection of motors. Please select the motor that best suits your needs to fully enjoy their unique character.
5. Characteristic Data for the ENERGY / TURBO / MAGNUM
6. Commentary of the Static Characteristic Data for the three motor types: ENERGY / TURBO / MAGNUM using a Dynamometer with an electric current brake to measure the different conditions as it passes 2V / 3V / 4V.
To prevent damage, we set the maximum measured electrical current at 45A.
- The Torque curve (in blue) displays torque vs. number of cycles.
- The Amps curve (in red) shows torque vs. electrical current.
- The Output curve (in green) shows torque vs. the output. These are all displayed accordingly.
The peak value is the data based on 45A.
The measurement results based on the motor’s performance rating is summarized below.
- Based on Speed: TURBO>ENERGY>MAGNUM
- Based on Torque: MAGNUM>ENERGY>TURBO
- Based on Output: MAGNUM>TURBO>ENERGY
- Passing the identical amount of electrical current in all of the motors it is very apparent that the overwhelming amount of cyclic revolutions came from the TURBO Motor.
- In addition, in terms of the number of cyclic revolutions between the ENERGY / MAGNUM Motors it is hardly a noticeable difference.
- With the identical amount of electrical current used for all of the motors, the MAGNUM Motor with it’s Neodymium Magnet produced the most amount of Torque.
- In terms of Torque, the ENERGY Motor slightly leads over the TURBO Motor.
- Furthermore, with the same amount of electrical current passing through, in terms of Output, the MAGNUM Motor has the best numerical value.
To summarize, for the MAGNUM / TURBO Motors, the torque value as well as the cyclic revolutions shows its projected performance, meanwhile the ENERGY Motor shows a very stable and well balanced motor that is adaptable to many different situations.